Supply and Installation of Triple Fire Pumps
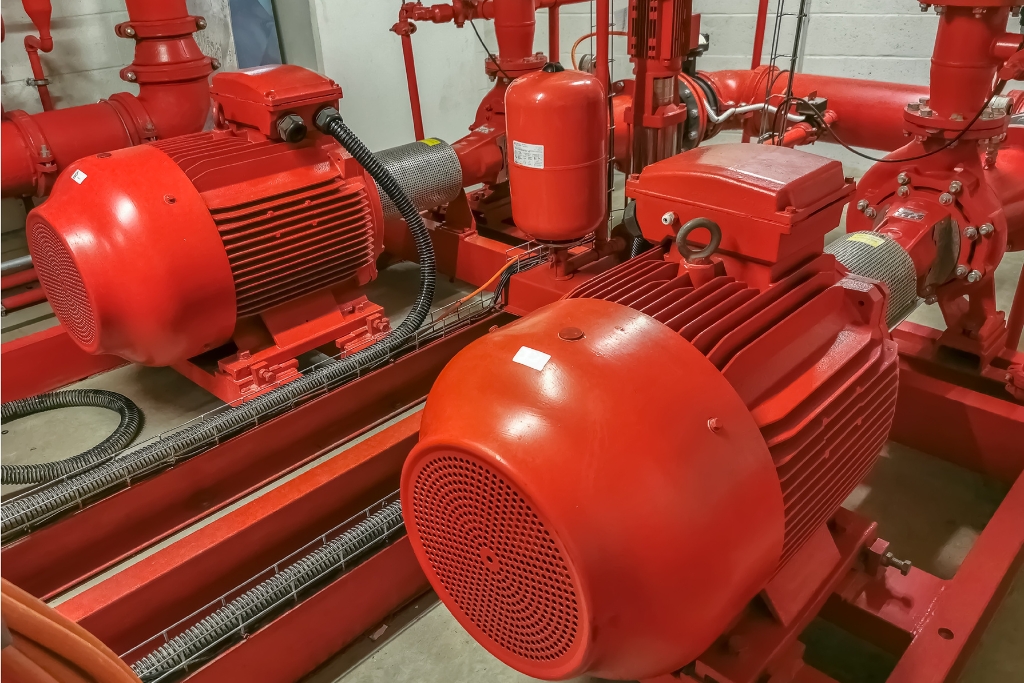

Fire pumps are an essential part of many water-based fire protection systems, they are used to increase the pressure (measured in psi and bar) of the water source. These are commonly found in buildings that tend to have high pressure demand such as high-rise buildings or storage warehouses.
There are many types of fire pumps available. It is important to choose the correct pump type for your installation project to avoid high costs, and to avoid excessive pressures that may damage your system. If all factors are not taken into account, this may result in a pump being installed that does not achieve the necessary pressure requirements which may require the installation of a new pump.
There are two main categories of pumps
Positive displacement pumps
Positive displacement pumps have a method of producing flow by capturing a specific amount of water per pump cycle and pushing it out through the discharge line. Positive displacement pumps create very high pressures but have limited flow volume compared to centrifugal pumps. These are not common because they have a specialized use, primarily with wet sprinklers and foam water systems.
Centrifugal pumps
Centrifugal pumps are the most common fire pumps and are used with most systems. With centrifugal pumps, pressure is developed primarily through the action of centrifugal or rotational force. Water in centrifugal pumps enters the suction inlet and passes to the center of the impeller. The rotation of the impeller in turn pushes the water by centrifugal force to the edge where it is discharged. Centrifugal pumps can handle large volumes of water while providing high-pressure boosts.
The following are different centrifugal type pump configurations:
Horizontal Split-Case Pump
With a horizontal split-case pump, the flow is split and enters the impeller from opposite
sides of the pump housing. As the name implies, this is a pump installed with a split casing
that can be opened for pump maintenance access and is connected to the driver by a
horizontal shaft.
They are very reliable, come in a wide range of rated flow and pressure capacities, are easy
to maintain due to their relatively easy split-case access, and can be used with both electric
and diesel drivers. However, these also typically need the most space of all types of fire
pumps.
Vertical Turbine Pump
A vertical turbine pump is the only type of pump allowed by NFPA 20, Standard for the Installation of Stationary Pumps for Fire Protection that can start with negative suction pressure or take water under a lift condition such as from a below grade source such as a river or subgrade tank. These pumps can be used with raw water sources such as ponds, lakes, and rivers. Vertical turbine pumps come in a wide range of capacities and pressures, and they can be used with diesel and electric drivers.
In-Line Pump
In-line pumps are useful where space is limited. These can be driven by both a vertical or horizontal shaft (end suction type). Vertical shaft types, which are the most common, have the driver located directly above the pump. These are typically one of the less expensive units and take the least amount of space but, they are also one of the more expensive to repair. Pump maintenance and repair can be difficult because the motor must be lifted off and removed to gain access to the pump, unlike a split-case unit. With these pumps, the suction flange and discharge flange are on approximately the same plane. In-line pumps have a limited capacity of typically no more than 1,500 gpm (5,678 L/min), and they can only be used with an electric driver which limits their potential applications.
End Suction Pump
An end suction pump has a discharge outlet perpendicular to the suction inlet. These pumps are typically limited to a capacity of approximately 1,500 gpm (5,678 L/min). Compared to horizontal split-case fire pumps, they are more compact and require less installation space in a fire pump room where available space is a concern. End suction pumps can be used with either an electric driver or a diesel driver.
Multistage Multiport Pump:
Multistage Multiport pumps use a single-driver that can be either an electric motor or a diesel engine that connects to a pump with multiple impellers in series in a single casing driven by a horizontal shaft. The casing has multiple ports, or discharge outlets, delivering different pressures - each port has increased pressure from the consecutive series impellers.